Aluminum coils come in several grades. These grades are based on their composition and manufacturing applications. These differences allow aluminum coils to be used by different industries. For example, some coils are harder than others, while others are more pliable. Knowing the required grade of aluminum also depends upon the fabrication and welding processes suitable for that aluminum type. Therefore, one would require understanding the area they want to apply the coil in order to pick the best grade of aluminum coil for their specific application.
1. 1000 Series Aluminum Coil
According to the worldwide brand name principle, a product must contain 99.5% or more aluminum to be approved as 1000 series aluminum, which is considered commercially pure aluminum. Despite not being heat-treatable, aluminum from the 1000 series has outstanding workability, excellent corrosion resistance, and high electrical and thermal conductivity. It can be welded, but only with specific precautions. Heating this aluminum does not alter its look. When welding this aluminum, it is significantly more difficult to distinguish between cold and hot material. 1050, 1100, and 1060 series make up most of the aluminum products on the market because they are the most pure.
● Typically, 1050, 1100 and 1060 aluminum is used to create cookware, curtain wall plates, and decorating elements for buildings.
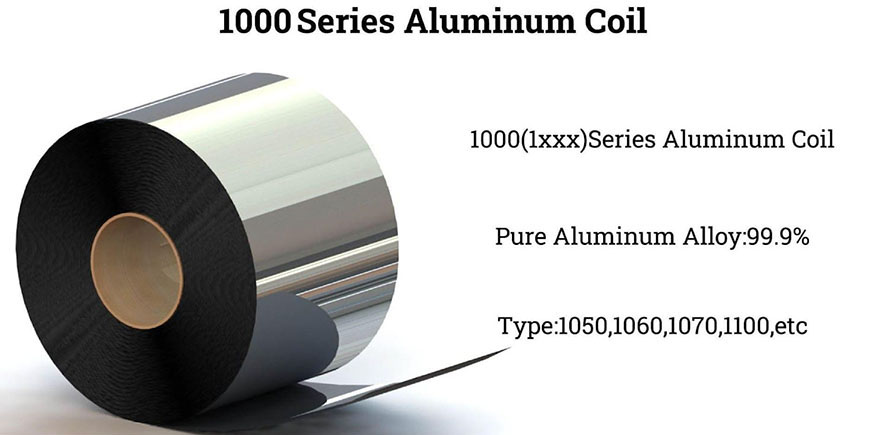
2. 2000 Series Aluminum Coil
Copper is added to the 2000 series aluminum coil, which then undergoes precipitation hardening to achieve steel-like strengths. The usual copper content of 2000 series aluminum coils ranges from 2% to 10%, with minor additions of other elements. It is extensively used in the aviation sector to make airplanes. This grade is employed here because of its availability and lightness.
● 2024 Aluminum
Copper serves as the main alloying ingredient in the 2024 aluminum alloy. It is utilized in situations where a high strength-to-weight ratio and superior fatigue resistance are necessary, such as in aircraft structural components like the fuselage and wing structures, carrying tension strains, aviation fittings, truck wheels, and hydraulic manifolds. It has a fair degree of machinability and can only be joined through friction welding.
3. 3000 Series Aluminum Coil
Manganese is rarely used as a principal alloying element and is only normally added to aluminum in small amounts. However, manganese is the primary alloying element in 3000 series aluminum alloys, and this series of aluminum is often non-heat treatable. As a result, this series of aluminum is more brittle than pure aluminum while being well-formed and resistant to corrosion. These alloys are good for welding and anodizing but cannot be heated. The alloys 3003 and 3004 make up most of the 3000 series aluminum coil. These two aluminums are used due to their strength, exceptional corrosion resistance, outstanding formability, good workability, and good “drawing” properties that make sheet metal forming processes easier. They have a wide range of applications. Beverage cans, chemical apparatus, hardware, storage containers, and lamp bases are some of the applications of 3003 and 3004 grades.
4. 4000 Series Aluminum Coil
The alloys of the 4000 series aluminum coil have fairly-high silicon concentrations and are not frequently utilized for extrusion. Instead, they are used for sheets, forgings, welding, and brazing. Aluminum's melting temperature is lowered, and its flexibility is raised by the addition of silicon. Due to these qualities, it is the ideal alloy for die casting.
5. 5000 Series Aluminum Coil
The distinguishing features of 5000 series aluminum coil are its smooth surface and exceptional deep-drawability. This alloy series is a popular option for various applications because it is significantly harder than other aluminum sheets. It is the perfect material for heat sinks and equipment casings due to its strength and fluidity. Furthermore, its excellent corrosion resistance is ideal for mobile homes, residential wall panels, and other applications. Aluminum magnesium alloys include 5052, 5005, and 5A05. These alloys are low in density and have strong tensile strength. As a result, they are found in many industrial applications and have a wide range of uses.
The 5000 series aluminum coil is a great option for most marine applications due to its significantly greater weight savings over other series of aluminum. The 5000 series aluminum sheet is. furthermore, a preferred option for marine applications since it is extremely resistant to acid and alkali corrosion.
● 5754 Aluminum Coil
Aluminum alloy 5754 principally contains magnesium and chromium. It cannot be created using casting methods; rolling, extrusion, and forging may be used to create it. Aluminum 5754 exhibits excellent corrosion resistance, particularly in the presence of seawater and industrially polluted air. Body panels and interior components for the automotive industry are typical usages. Additionally, it can be applied to flooring, shipbuilding, and food processing applications.
6. 6000 Series Aluminum Coil
6000 series aluminum alloy coil is represented by 6061, which is mostly composed of silicon and magnesium atoms. 6061 aluminum coil is a cold-treated aluminum forging product which is appropriate for applications needing a high oxidation and corrosion resistance level. It possesses great interface properties, facile coating, and good workability, in addition to good serviceability. It can be applied to aircraft joints and low-pressure armaments. It can counteract the negative effects of iron due to its particular content of manganese and chromium. Occasionally, a small amount of copper or zinc is added to boost the alloy's strength without considerably lowering its corrosion resistance. Excellent interface properties, ease of coating, high strength, outstanding serviceability, and strong corrosion resistance are among the general qualities of 6000 aluminum coils.
Aluminum 6062 is a wrought aluminum alloy featuring magnesium silicide. It responds to heat treatment to age-harden it. This grade can be used in the manufacture of submarines because of its corrosion- resistance in fresh and saltwater.
7. 7000 Series Aluminum Coil
For aeronautical applications, 7000 series aluminum coil is very beneficial. Thanks to its low melting point and great corrosion resistance, it works well with applications requiring these traits. However, there are some significant distinctions between these various aluminum coil types. Al-Zn-Mg-Cu series alloys make up the majority of the 7000 series aluminum alloys. The aerospace industry and other high-demand industries favor these alloys because they provide the maximum strength of all aluminum series. In addition, they are perfect for various manufacturing applications due to their high hardness and resistance to corrosion. These aluminum alloys are used in various radiators, aircraft parts, and other things.
● 7075 Series Aluminum Coil
Zinc serves as the main alloying ingredient in the 7075 aluminum alloy. It demonstrates exceptional ductility, high strength, toughness, and good resistance to fatigue in addition to having outstanding mechanical qualities.
7075 series aluminum coil is frequently employed for the production of airplane parts like wings and fuselages. In other industries, its strength and small weight are also advantageous. Aluminum alloy 7075 is frequently used to make bicycle parts and equipment for rock climbing.
8. 8000 Series Aluminum Alloy Coil
Another of the many models of aluminum coil is the 8000 series. Mostly lithium and tin make up the mix of alloys in this series of aluminum. Other metals can also be added to effectively increase the stiffness of the aluminum coil and improve the metal properties of the 8000 series aluminum coil.
High strength and outstanding formability are features of the 8000 series aluminum alloy coil. The other beneficial characteristics of the 8000 series include high-corrosion resistance, excellent electrical conductivity and bending ability, and less metallic weight. The 8000 series is usually applied in areas where there is a need for high electrical conductivity such as electrical cable wires.
We Jindalai Steel Group have customer from Philippines, Thane, Mexico, Turkey, Pakistan, Oman, Israel, Egypt, Arab, Vietnam, Myanmar, India etc. Send your inquiry and we will be happy to consult you professionally.
HOTLINE: +86 18864971774 WECHAT: +86 18864971774 WHATSAPP: https://wa.me/8618864971774
EMAIL: jindalaisteel@gmail.com sales@jindalaisteelgroup.com WEBSITE: www.jindalaisteel.com
Post time: Dec-19-2022